Coca-Cola Europe: Chemical Recall
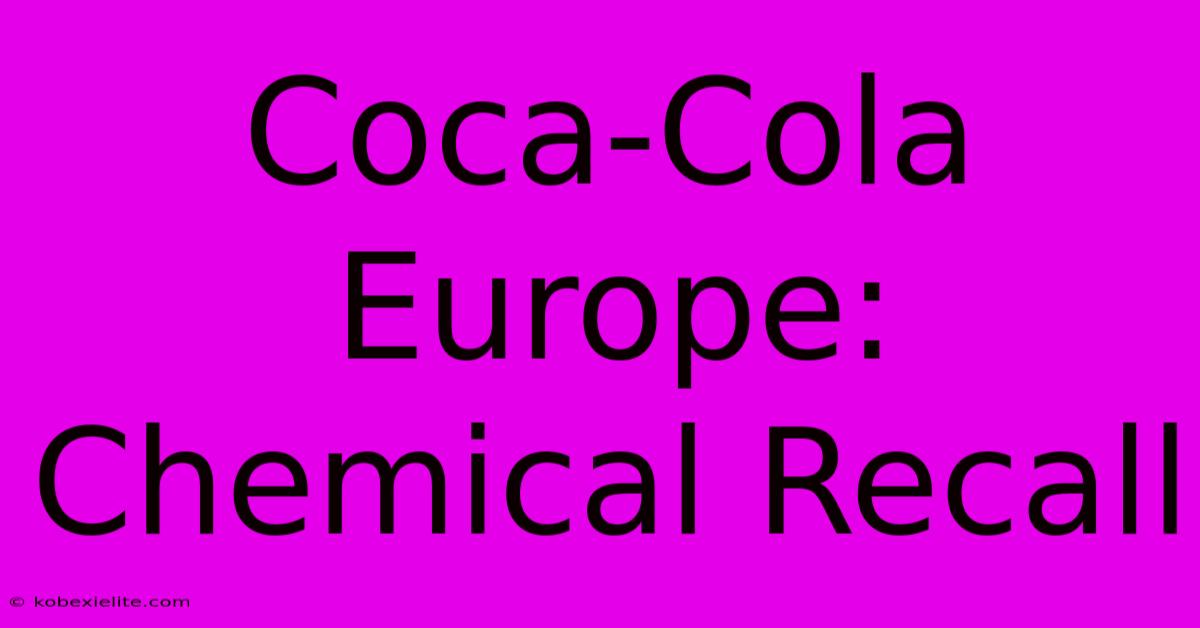
Discover more detailed and exciting information on our website. Click the link below to start your adventure: Visit Best Website mr.cleine.com. Don't miss out!
Table of Contents
Coca-Cola Europe: Chemical Recall โ What Happened and What We Know
The beverage industry, particularly giants like Coca-Cola, operates under intense scrutiny. Any hint of contamination or safety concerns can lead to widespread panic and significant damage to brand reputation. In recent years, there haven't been major chemical recalls impacting Coca-Cola products in Europe on the scale of a widespread, multi-product crisis. However, understanding potential risks and how Coca-Cola addresses them is crucial. This article explores past incidents, potential chemical hazards, and the company's safety protocols.
Understanding Potential Chemical Hazards in Soft Drinks
Before diving into specific recall scenarios, let's examine potential chemical hazards that could impact soft drinks like Coca-Cola:
- Pesticide Residues: Agricultural products used in ingredient sourcing (e.g., fruits, sugar cane) could contain pesticide residues. Stringent testing and supplier regulations are vital to mitigate this.
- Heavy Metals: Contamination from processing equipment or water sources could introduce heavy metals like lead or cadmium into the final product.
- Microbial Contamination: Bacteria or mold could contaminate the product at various stages of production, packaging, or distribution. This necessitates rigorous hygiene protocols.
- Packaging Issues: Chemicals from packaging materials could leach into the beverage, particularly if storage or handling conditions aren't optimal.
Coca-Cola's Safety Procedures and Quality Control
Coca-Cola, like other large food and beverage companies, maintains extensive quality control measures to minimize risks. These typically include:
- Stringent Supplier Audits: Thorough inspections of ingredient suppliers to ensure adherence to safety and quality standards.
- Regular Testing: Multiple checks throughout the production process to detect any contamination or deviations from specifications.
- Traceability Systems: Sophisticated systems to track ingredients and products throughout the entire supply chain, facilitating quick identification and removal of contaminated batches if necessary.
- Consumer Complaint Mechanisms: Clear procedures for handling consumer complaints and reporting potential problems.
- Compliance with Regulations: Adherence to all relevant food safety regulations and standards set by European Union (EU) authorities and individual member states.
Addressing Past Incidents (If Any) and Transparency
While no large-scale chemical recall specifically involving Coca-Cola in Europe has dominated headlines recently, it's crucial to note that smaller, localized incidents are possible. Transparency in handling such situations is vital. If a problem arises, the company's actions will be carefully examined by consumers, regulatory bodies, and the media. Successful crisis management involves swift action, open communication, and a commitment to consumer safety.
Best Practices for Consumers
While Coca-Cola implements extensive safety measures, consumers can also take precautions:
- Check Packaging: Inspect packaging for any signs of damage or unusual characteristics.
- Report Concerns: Contact Coca-Cola customer service immediately if you suspect any problems with a product.
- Be Aware of Expiry Dates: Consume products before their expiry date to minimize the risk of spoilage.
Conclusion: Proactive Measures and Consumer Confidence
The absence of recent major chemical recalls for Coca-Cola in Europe is indicative of the company's robust safety protocols. However, vigilance remains key. Ongoing investment in quality control, transparent communication, and proactive risk management are essential for maintaining consumer confidence and safeguarding public health. The company's commitment to these practices is crucial for its long-term success. Continuous improvement and adaptation to evolving safety standards are necessary to prevent future incidents and protect the brand's reputation.
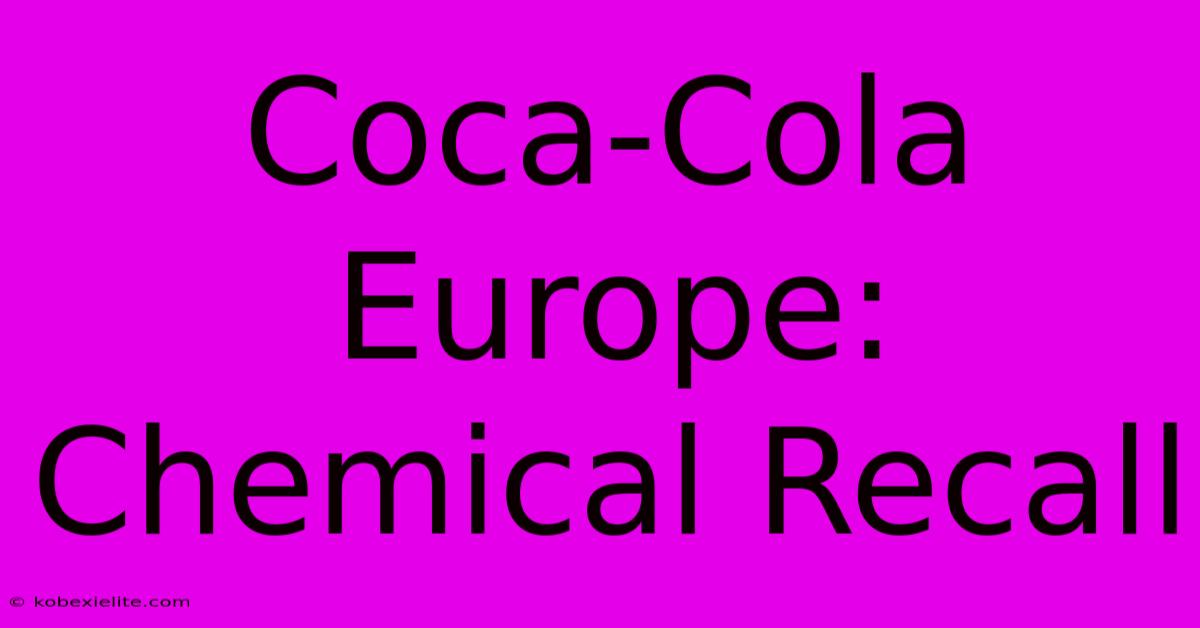
Thank you for visiting our website wich cover about Coca-Cola Europe: Chemical Recall. We hope the information provided has been useful to you. Feel free to contact us if you have any questions or need further assistance. See you next time and dont miss to bookmark.
Featured Posts
-
Genocide Hotline Mintos Stand
Jan 28, 2025
-
The Punisher Found Dead Victorian Era
Jan 28, 2025
-
Jota Felipe Returns To Celtic Fc
Jan 28, 2025
-
Remembering The Vivienne
Jan 28, 2025
-
Mitch Owens Bbl Century Record
Jan 28, 2025