Same Old, Same Old: Wasteful Finishing
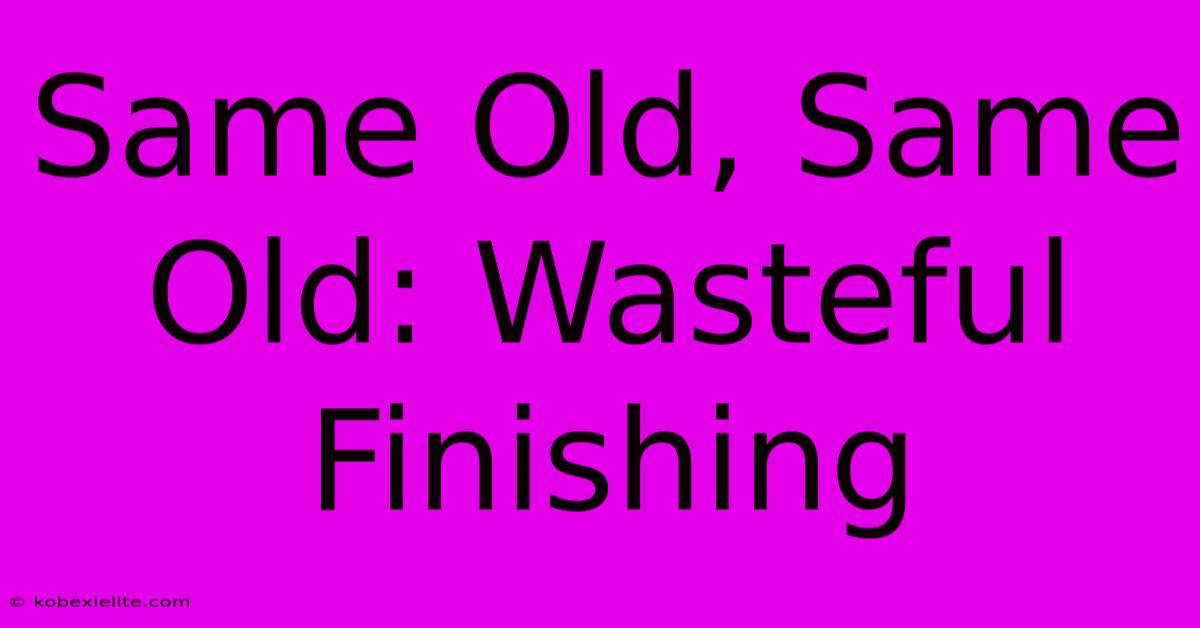
Discover more detailed and exciting information on our website. Click the link below to start your adventure: Visit Best Website mr.cleine.com. Don't miss out!
Table of Contents
Same Old, Same Old: Wasteful Finishing โ Time to Revamp Your Processes
Are you tired of the same old, same old when it comes to finishing your products? Do you find yourself consistently battling excessive material waste, inefficient processes, and ultimately, a hit to your bottom line? You're not alone. Many manufacturers struggle with wasteful finishing practices, impacting both profitability and sustainability. This article will delve into the common culprits of wasteful finishing and offer practical strategies to optimize your processes.
Identifying the Sources of Wasteful Finishing
Before you can fix a problem, you need to understand it. Let's pinpoint some common areas where finishing processes often fall short:
1. Material Waste:
- Over-application of finishes: Applying too much coating, paint, or other materials leads to excess usage and increased costs. This can also affect the final product's quality, leading to defects and rework.
- Poor material handling: Inefficient storage, improper mixing, and inadequate dispensing techniques contribute to significant material loss. Spills, drips, and evaporation are all common issues.
- Lack of precision cutting: Improperly sized or cut materials require more finishing processes and inevitably lead to scrap.
- Inconsistent material quality: Using materials that are not consistently uniform can lead to uneven application and increased waste.
2. Inefficient Processes:
- Outdated equipment: Using old, inefficient finishing equipment increases processing time and material waste. Modern technologies offer significant improvements in precision and efficiency.
- Lack of process optimization: Failing to analyze and refine your finishing process can lead to bottlenecks, rework, and overall inefficiency.
- Inadequate training: Improperly trained personnel can lead to errors, rework, and increased material consumption.
- Poor workflow: A poorly designed workflow can lead to delays, bottlenecks, and increased waste.
3. Energy Consumption:
- High energy-consuming equipment: Outdated or inefficient equipment consumes more energy, increasing operational costs and your carbon footprint.
- Poorly insulated facilities: Lack of proper insulation leads to energy loss and higher energy bills.
- Inefficient drying processes: Using energy-intensive drying methods can significantly increase energy consumption.
Strategies for a More Efficient Finishing Process
Now that we've identified the culprits, let's look at actionable strategies to improve your finishing processes:
1. Embrace Lean Manufacturing Principles:
Implementing lean manufacturing principles can significantly reduce waste in your finishing process. Focus on eliminating non-value-added activities, identifying and eliminating bottlenecks, and improving workflow efficiency.
2. Invest in Modern Equipment:
Modern finishing equipment is often more precise, efficient, and less wasteful. Consider upgrading your equipment to improve your processes. Look for equipment with features that minimize overspray, optimize material usage, and offer precise control.
3. Optimize Material Handling:
Implement a robust material handling system to minimize spills, waste, and evaporation. Proper storage, dispensing techniques, and material tracking can greatly improve efficiency.
4. Invest in Employee Training:
Proper training is key to reducing waste and improving efficiency. Ensure your employees are properly trained on the safe and efficient use of equipment and materials. Regular training and refresher courses can keep your team up-to-date on best practices.
5. Implement a Quality Control System:
A robust quality control system can identify and address problems early in the finishing process, preventing defects and rework. This includes regular inspections, testing, and feedback mechanisms.
6. Explore Sustainable Finishing Options:
Consider using water-based or other eco-friendly finishes to reduce your environmental impact and potentially lower costs in the long run.
The Bottom Line: Wasteful Finishing Doesn't Have to Be the Norm
Switching from "same old, same old" to a more efficient and sustainable finishing process requires a proactive approach. By identifying areas for improvement, investing in technology and training, and implementing lean principles, you can significantly reduce waste, improve profitability, and enhance your company's environmental responsibility. Don't let wasteful finishing practices continue to drain your resources โ take action today!
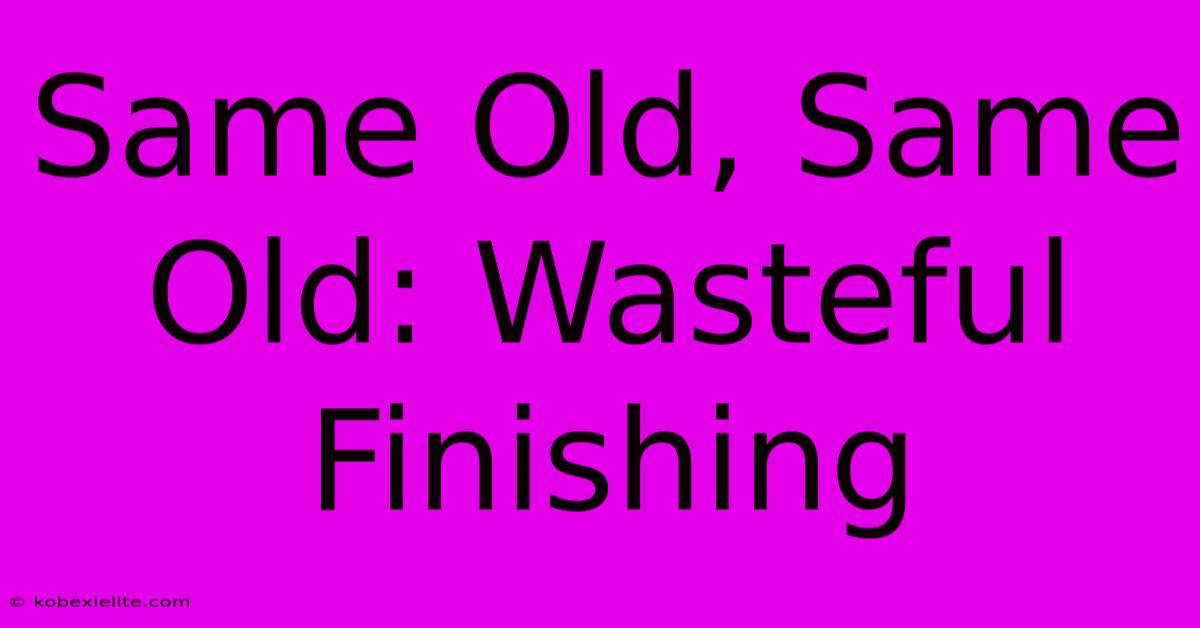
Thank you for visiting our website wich cover about Same Old, Same Old: Wasteful Finishing. We hope the information provided has been useful to you. Feel free to contact us if you have any questions or need further assistance. See you next time and dont miss to bookmark.
Featured Posts
-
Ryan Reynolds Snl Lawsuit Sketch
Feb 18, 2025
-
Late Subs Cost Inter The Title
Feb 18, 2025
-
La Liga Match Barcelona Defeats Rayo 1 0
Feb 18, 2025
-
Mortgage Holders Eye Rba Rate Reduction
Feb 18, 2025
-
Gabby Petito Netflix Documentary Reveals
Feb 18, 2025