Avoid Wasteful Finishing: Improve Efficiency
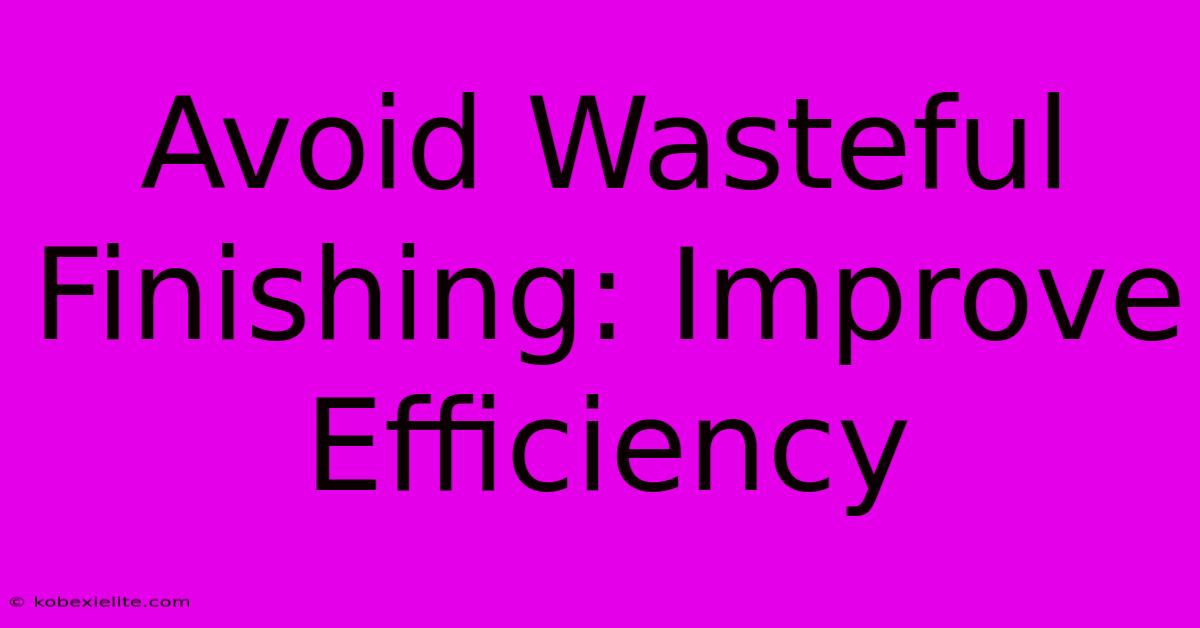
Discover more detailed and exciting information on our website. Click the link below to start your adventure: Visit Best Website mr.cleine.com. Don't miss out!
Table of Contents
Avoid Wasteful Finishing: Improve Efficiency
In today's competitive business landscape, efficiency is paramount. Every aspect of your operation, from raw material sourcing to final product delivery, needs to be streamlined for maximum profitability. One often-overlooked area where significant improvements can be made is finishing processes. Wasteful finishing practices can significantly impact your bottom line, leading to lost time, increased costs, and reduced overall productivity. This article explores key strategies to identify and eliminate wasteful finishing, leading to improved efficiency and enhanced profitability.
Understanding Wasteful Finishing Practices
Before we delve into solutions, it's crucial to understand what constitutes wasteful finishing. This goes beyond simply discarding defective products. It encompasses a broader range of inefficiencies, including:
-
Excessive Material Use: Using more materials than necessary, leading to higher raw material costs and waste disposal fees. This could involve improper cutting, inefficient application techniques, or a lack of precise measurement.
-
Inefficient Processes: Slow, cumbersome finishing processes that consume excessive time and labor. This includes poorly designed workflows, inadequate equipment, or a lack of proper training for your team.
-
High Defect Rates: A high percentage of defective products requiring rework or scrapping, leading to material waste and increased production time. This often stems from poor quality control measures or inadequately trained personnel.
-
Poor Inventory Management: Overstocking of finishing materials, leading to increased storage costs and potential spoilage. Conversely, insufficient stock can cause production delays.
-
Lack of Optimization: Failing to regularly assess and optimize your finishing processes to identify and address bottlenecks or inefficiencies.
Strategies to Minimize Wasteful Finishing
Implementing the following strategies can significantly reduce wasteful finishing practices and boost your efficiency:
1. Optimize Material Usage:
-
Precise Measurement & Cutting: Invest in accurate measuring tools and techniques to minimize material waste during the cutting and shaping stages. Consider using specialized software for optimized cutting patterns.
-
Lean Manufacturing Principles: Employ lean manufacturing principles to eliminate unnecessary steps and reduce material consumption. This includes techniques like 5S (Sort, Set in Order, Shine, Standardize, Sustain) and Kaizen (continuous improvement).
-
Material Selection: Choose materials wisely, considering their properties and suitability for the finishing process to reduce waste from material defects or incompatibility.
2. Streamline Finishing Processes:
-
Process Mapping & Analysis: Create detailed process maps to identify bottlenecks and areas for improvement. This allows for targeted optimization efforts.
-
Automation & Technology: Explore opportunities to automate repetitive finishing tasks, increasing speed and consistency while reducing human error. Consider investing in advanced finishing equipment.
-
Employee Training: Provide thorough training to your staff on proper finishing techniques, equipment operation, and quality control procedures.
3. Implement Robust Quality Control:
-
Regular Inspections: Implement regular inspections throughout the finishing process to identify and address defects early, minimizing rework and waste.
-
Statistical Process Control (SPC): Use SPC methods to monitor and control variations in the finishing process, leading to improved consistency and reduced defects.
-
Preventive Maintenance: Regularly maintain and calibrate your finishing equipment to prevent breakdowns and ensure optimal performance.
4. Improve Inventory Management:
-
Just-in-Time (JIT) Inventory: Adopt a JIT inventory system to minimize storage costs and reduce the risk of spoilage.
-
Inventory Tracking: Implement robust inventory tracking systems to ensure accurate stock levels and prevent shortages or overstocking.
5. Continuous Improvement:
-
Regular Reviews: Regularly review your finishing processes to identify areas for ongoing improvement.
-
Data Analysis: Use data analysis to track key metrics such as material waste, defect rates, and production time to monitor progress and identify areas needing attention.
By implementing these strategies, you can effectively minimize wasteful finishing practices, leading to increased efficiency, reduced costs, improved product quality, and enhanced profitability. Remember, a commitment to continuous improvement is key to maintaining a lean and efficient finishing process. Start by analyzing your current processes, identify the biggest areas of waste, and implement targeted solutions. The results will speak for themselves.
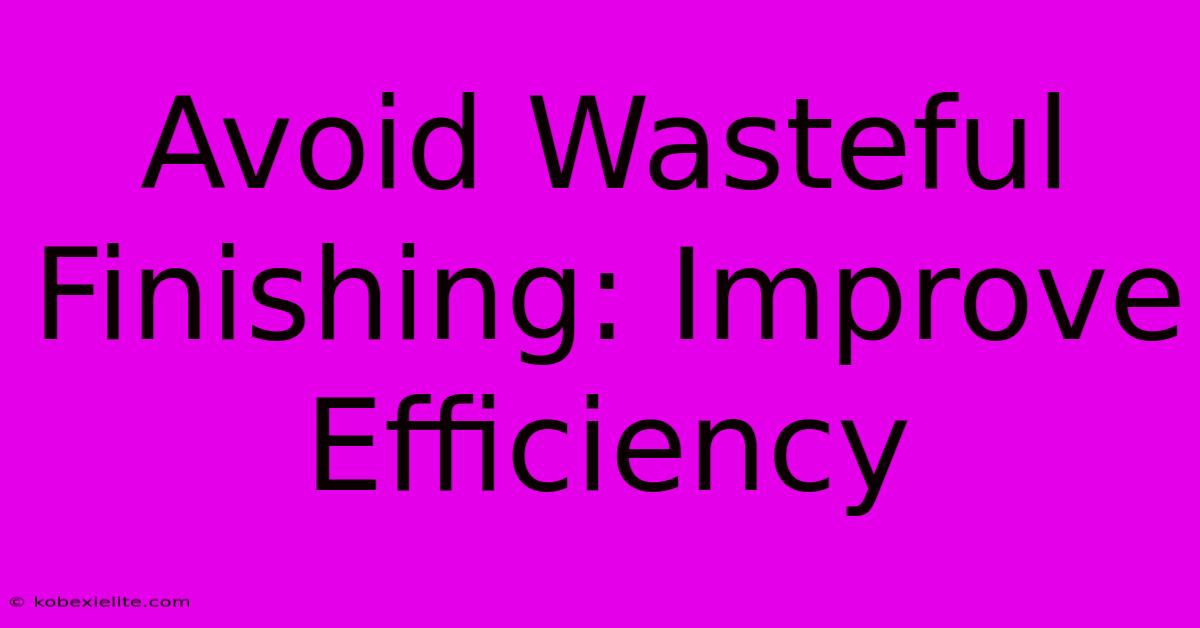
Thank you for visiting our website wich cover about Avoid Wasteful Finishing: Improve Efficiency. We hope the information provided has been useful to you. Feel free to contact us if you have any questions or need further assistance. See you next time and dont miss to bookmark.
Featured Posts
-
Barcelona Vs Rayo Kick Off Time And Venue
Feb 18, 2025
-
Petito Murder Netflix Doc Exposes
Feb 18, 2025
-
Same Old Same Old Wasteful Finishing
Feb 18, 2025
-
Genesis Invitational Abergs Victory
Feb 18, 2025
-
Jack Nicholson Introduces Adam Sandler
Feb 18, 2025